Table of contents
Axial cylindrical roller bearings
- Bearing design
- Load carrying capacity
- Compensation of angular misalignments
- Lubrication
- Sealing
- Speeds
- Noise
- Temperature range
- Cages
- Internal clearance
- Dimensions, tolerances
- Suffixes
- Structure of bearing designation
- Dimensioning
- Minimum load
- Design of bearing arrangements
- Mounting and dismounting
- Legal notice regarding data freshness
- Further information
Axial cylindrical roller bearings
Single and double row axial cylindrical roller bearings are particularly suitable where:
- high axial and shock loads occur in one direction but no radial loads are present ➤ Figure and ➤ section
- the load carrying capacity of the corresponding axial deep groove ball bearings is no longer adequate (in this case, bearings of series 811 and 812 are especially suitable)➤ Figure
- the bearing arrangement must have very high axial rigidity
- the axial space available is very small ➤ Figure and ➤ dimension table
- the bearing arrangement can be configured, where the axial space is very small, as a direct bearing arrangement ➤ section
- the bearing parts can or must be mounted separately
- the bearing arrangement is not configured in itself but, for cost reasons, ready-to-fit standard bearings are to be used
Axial cylindrical roller bearing and axial ball bearing – comparison of load carrying capacity and design envelope Fa = axial load Ca = basic dynamic load rating Dw = roller diameter T = axial section height of axial deep groove ball bearing |
![]() |
Bearing design
Design variants
Axial cylindrical roller bearings are available as:
- single and double row bearings
Larger catalogue bearings and other bearing designs GL 1.
Axial cylindrical roller bearings
Designed for bearing arrangements with very small axial space
Axial cylindrical roller bearings are part of the group of axial roller bearings. In contrast to the ball, the roller has a larger contact area perpendicular to the roller axis. As a result, it can transmit higher forces, has greater rigidity and allows smaller rolling element diameters under the same load. The single and double row bearings comprise flat, ribless washers (housing and shaft locating washers) between which axial cylindrical roller and cage assemblies are arranged ➤ Figure and ➤ Figure. Their axial section height T corresponds only to the diameter of the rollers plus the thickness of the washers. Due to this design, the bearings are particularly small in axial height ➤ dimension table. The axial cages are made from brass or plastic and are fitted with one or two rows of cylindrical rollers. Since sliding occurs towards the ends of the rollers during rolling of the rolling elements and this increases with the length of the roller, bearings with a wide cross-section have several short rollers arranged adjacent to each other, e. g. double row designs ➤ Figure.
Rollers with profiled ends increase the operating life of the bearings
The cylindrical rollers have profiled ends, i. e. they have a slight lateral curvature towards the ends. This modified line contact between the rollers and raceways prevents damaging edge stresses ➤ Figure. This in turn has a positive effect on the operating life of the bearings.
The use of complete axial cylindrical roller bearings (shaft locating washer, axial cylindrical roller and cage assembly and housing locating washer) is then advisable if, for example, high speeds occur and the bearing washers must therefore be centred precisely.
Roller and cage assembly and bearing washers are also available individually
The bearing parts for axial cylindrical roller bearings are also available individually ➤ Figure and ➤ Figure. Axial cylindrical roller and cage assemblies (without shaft and housing locating washers) are suitable, for example, for bearing arrangements with very small axial design space.
Cylindrical roller bearings 811 and 812 are of a single row design and correspond to DIN 722:2005 and ISO 104:2015. The bearings 893 and 894 are of a double row design and are configured in accordance with DIN 616:2000 and ISO 104:2015.
Axial cylindrical roller bearings Fa = axial load
|
![]() |
Roller profile and stress distribution
|
![]() |
Axial cylindrical roller and cage assemblies
Very high axial load carrying capacity with low section height
The cage assemblies comprise axial cages and one or two rows of cylindrical rollers ➤ Figure. They have a particularly small axial section height and high axial load carrying capacity. The cages are made from polyamide or brass and are guided on the shaft.
For direct bearing arrangements, running surfaces must be produced as a rolling bearing raceway
Axial cylindrical roller and cage assemblies are generally combined with one housing locating washer and one shaft locating washer. If they are to be used directly – i. e. without axial bearing washers – in the adjacent construction, the raceway for the rollers must be produced as a rolling bearing raceway ➤ section. It is also possible to use two shaft locating washers or two housing locating washers in combination with one axial cylindrical roller and cage assembly.
The diameter series 1, 2, 3, 4 of the axial cylindrical roller and cage assemblies correspond to DIN 616:2000 and ISO 104:2015.
Axial cylindrical roller and cage assemblies Fa = axial load
|
![]() |
Axial bearing washers
Housing and shaft locating washers
Housing locating washers are externally centred, shaft locating washers are internally centred ➤ Figure and ➤ section. They must be used if the adjacent construction cannot be used as a raceway for the rolling elements. The washers are made from through-hardening rolling bearing steel. The bore and outside diameter are precision machined, the raceways are ground to high accuracy.
The diameter series 1, 2, 3, 4 of the axial bearing washers correspond to DIN 616:2000 and ISO 104:2015.
Bearing washers
Bearing washers are suitable for use as a housing or shaft locating washer. They are used in applications that do not require precise centring of the axial bearing washers. The raceway of the bearing washers is hardened and ground. The bearing washers are suitable for axial cylindrical roller and cage assemblies K811 and axial needle roller and cage assemblies AXK.
Axial bearing washers
|
![]() |
Load carrying capacity
For very high axial loads acting in one direction
Single and double row axial cylindrical roller bearings can support high axial loads as well as axial shock loads in one direction, but must not be subjected to radial load ➤ section. If radial loads do occur, these forces must be supported by an additional bearing (e. g. by a needle roller and cage assembly) ➤ Figure.
Axial and radial loads Fr = radial load Fa = axial load
|
![]() |
Compensation of angular misalignments
The bearings do not permit any skewing between the shaft and the housing. If angular misalignments occur between the locating surfaces on the shaft and in the housing, this will cause damage to the bearing and considerably reduce its operating life.
Lubrication
Oil or grease lubrication is possible
Axial cylindrical roller bearings are not greased. The bearings must be lubricated with oil or grease.
Compatibility with plastic cages
When using bearings with plastic cages, compatibility between the lubricant and the cage material must be ensured if synthetic oils, lubricating greases with a synthetic oil base or lubricants containing a high proportion of EP additives are used.
If there is any uncertainty regarding the suitability of the selected lubricant for the application, please consult Schaeffler or the lubricant manufacturer.
Observe oil change intervals
Aged oil and additives in the oil can impair the operating life of plastics at high temperatures. As a result, stipulated oil change intervals must be strictly observed.
Sealing
Provide seals in the adjacent construction
The bearings are not sealed; i. e. sealing of the bearing position must be carried out in the adjacent construction. This must reliably prevent:
- moisture and contaminants from entering the bearing
- the egress of lubricant from the bearing position
Speeds
Limiting speeds and reference speeds in the product tables
Two speeds are generally indicated in the product tables ➤ dimension table:
- the kinematic limiting speed nG
- the thermal speed rating nϑr
Limiting speed
The limiting speed nG is the kinematically permissible speed of a bearing. Even under favourable mounting and operating conditions, this value should not be exceeded without prior consultation with Schaeffler ➤ link. The values in the product tables are valid for oil lubrication.
Values for grease lubrication
For grease lubrication, 25% of the value stated in the product tables is permissible in each case.
Reference speeds
nϑr is used to calculate nϑ
The thermal speed rating nϑr is not an application-oriented speed limit, but is a calculated ancillary value for determining the thermally safe operating speed nϑ ➤ link.
Noise
Schaeffler Noise Index
The Schaeffler Noise Index (SGI) is not yet available for this bearing type ➤ link. The data for these bearing series will be introduced and updated in stages.
Temperature range
Limiting values
The operating temperature of the bearings is limited by:
- the dimensional stability of the bearing washers and cylindrical rollers
- the cage
- the lubricant
Possible operating temperatures of axial cylindrical roller bearings ➤ Table.
Permissible temperature range
Operating temperature |
Axial cylindrical roller bearings |
---|---|
|
–20 °C to +120 °C |
In the event of anticipated temperatures which lie outside the stated values, please contact Schaeffler.
Cages
Solid cages made from brass and polyamide PA66 are used as standard
Standard cages ➤ Table . The cage design is dependent on the bearing series and the bearing size. Other cage designs are available by agreement. With such cages, however, suitability for high speeds and temperatures as well as the basic load ratings may differ from the values for the bearings with standard cages.
For high continuous temperatures and applications with difficult operating conditions, bearings with brass cages should be used. If there is any uncertainty regarding cage suitability, please consult Schaeffler.
Cage, cage suffix, bore code
Bearing series |
Solid cage |
Solid brass cage |
---|---|---|
TV |
M |
|
standard |
standard |
|
Bore code |
||
811, K811 |
up to 34 |
from 36 |
812, K812 |
06 to 26 |
from 28 |
893, K893 |
06 to 16 |
17 to 30 |
894, K894 |
12 to 14 |
from 15 |
Internal clearance
Axial clearance and preload are determined by the application
In the case of axial cylindrical roller bearings, the internal clearance (axial clearance) is only achieved when the bearings are mounted. The requisite axial clearance of the bearing arrangement is dependent on the application and must take account of the conditions in the bearing arrangement while warm from operation and subjected to load. If axial cylindrical roller bearings are subjected to vibrations while under predominantly static load, for example, they must be lightly preloaded. Preload can be applied, for example, using calibrated sheets (shims) ➤ Figure. Other suitable means include shaft nuts, disc springs, etc. ➤ section. It must always be ensured that no slippage occurs in operation between the rolling elements and raceways ➤ section. It must also be ensured that the preload does not exceed the optimum value, otherwise there will be an increase in friction and therefore in heat generation in the bearing. These will both have a negative effect on the operating life of the bearings.
If there is any uncertainty regarding correct setting, please consult Schaeffler.
Setting of the axial clearance by means of shims
|
![]() |
Dimensions, tolerances
Dimension standards
The main dimensions of axial cylindrical roller bearings correspond to ISO 104:2015.
Chamfer dimensions
The limiting dimensions for chamfer dimensions correspond to DIN 620‑6:2004. Overview and limiting values ➤ link. Nominal value of chamfer dimension ➤ dimension table.
Tolerances
The dimensional and running tolerances of axial bearing washers GS and WS correspond to the tolerance class Normal in accordance with ISO 199:2014 ➤ Table to ➤ Table.
Tolerances of the bore and outside diameter as well as of the width of the bearing parts ➤ Table and ➤ Figure.
Dimensions and tolerances of bearing parts
Bearing component |
Dimension |
Tolerance |
---|---|---|
Axial cylindrical roller and |
Dc1 |
E11 |
Dc |
a13 |
|
Dw |
to DIN 5402-1 |
|
Housing locating washer GS |
D1 |
‒ |
D |
to ISO 199 |
|
B |
h11 |
|
Shaft locating washer WS |
d |
to ISO 199 |
d1 |
‒ |
|
B |
h11 |
|
Bearing washer LS |
d |
E12 |
D |
a12 |
|
B |
h11 |
Deviation of the bore diameter Δdmp and deviation of the outside diameter ΔDmp ➤ link.
Bearing parts – axial cylindrical roller and cage assemblies and bearing washers |
![]() |
Suffixes
For a description of the suffixes used in this chapter ➤ Table and medias interchange http://www.schaeffler.de/std/1B69.
Suffixes and corresponding descriptions
Suffix |
Description of suffix |
|
---|---|---|
M |
Solid brass cage |
Standard, |
TV |
Solid cage made from glass fibre reinforced polyamide PA66 |
|
P5 |
High dimensional, geometrical and running accuracy |
Special design |
Structure of bearing designation
Examples of composition of bearing designation
The designation of bearings follows a set model. Examples ➤ Figure and ➤ Figure. The composition of the designation is subject to DIN 623-1 ➤ Figure.
Single row axial cylindrical roller bearing, comprising axial roller and cage assembly, shaft locating washer and housing locating washer: designation structure |
![]() |
Double row axial cylindrical roller bearing, comprising axial roller and cage assembly, shaft locating washer and housing locating washer: designation structure |
![]() |
Dimensioning
Equivalent dynamic bearing load
Axial cylindrical roller bearings can only support axial forces ➤ section. In the rating life equation, P is therefore substituted by the value for Fa ➤ Equation.
Equivalent dynamic load
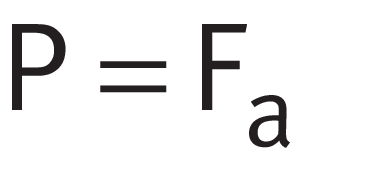
Legend
P | N |
Equivalent dynamic bearing load |
Fa | N |
Axial load. |
Equivalent static bearing load
Combined loads are not possible
In relation to the direction of load, the same conditions apply as for the equivalent dynamic bearing load, i. e. combined loads are not permissible. In the rating life equation, P0 is therefore substituted by the value for F0a ➤ Equation.
Equivalent static load
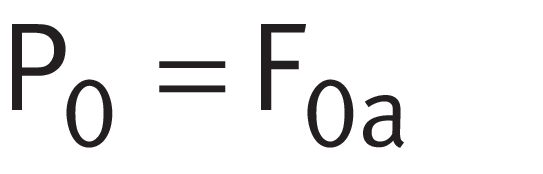
Legend
P0 | N |
Equivalent static bearing load |
F0a | N |
Largest axial load present (maximum load). |
Static load safety factor
S0 = C0/P0
In addition to the basic rating life L (L10h), it is also always necessary to check the static load safety factor S0 ➤ Equation.
Static load safety factor
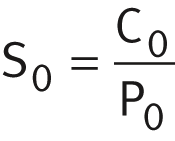
Legend
S0 |
Static load safety factor |
|
C0 | N |
Basic static load rating |
P0 | N |
Equivalent static bearing load. |
Minimum load
Rolling bearings under low loads are particularly prone to slippage
In order to prevent slippage damage, the bearing must be subjected to a minimum axial load Fa min ➤ Equation and ➤ Table. In vertical bearing arrangements in particular, the requisite minimum axial load Fa min is normally achieved, however, simply by the weight of the bearing parts and the external forces. If this is not the case, the bearing arrangement must be preloaded, for example by means of springs or a housing nut.
Minimum axial load
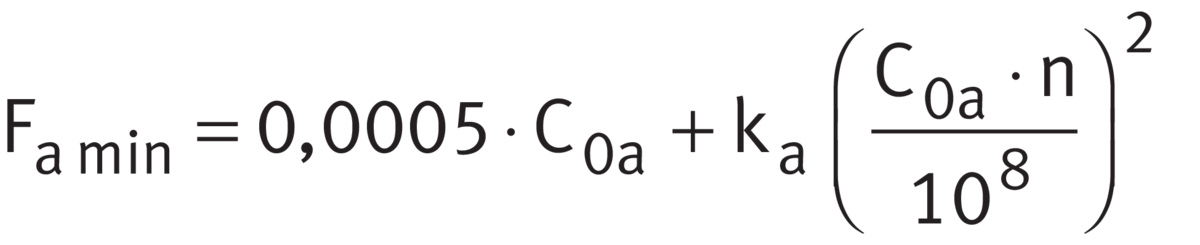
Legend
Fa min | N |
Minimum axial load |
C0a | N |
Basic static load rating ➤ dimension table |
ka |
Factor for determining the minimum axial load ➤ Table |
|
n | min–1 |
Speed. |
Factor ka for calculating the minimum axial load
Series |
Factor ka |
---|---|
K811 |
1,4 |
K812 |
0,9 |
K893 |
0,7 |
K894 |
0,5 |
Design of bearing arrangements
Design of adjacent parts
Axial cylindrical roller bearings cannot tolerate angular misalignments ➤ section. The locating surfaces for the bearing parts on the shaft and in the housing must therefore be vertical to the shaft axis, while the adjacent parts must be rigid and flat. They must be configured such that the bearing washers are supported as far as possible over the whole circumference and over the whole raceway width; values ➤ dimension table. The radial cage guidance surfaces must be precision machined and wear-resistant (Ramax 0,8(Rzmax 4)).
Mounting diameter on the shaft and in the housing
For the mounting dimensions, the following values apply ➤ dimension table:
- mounting diameter on the shaft ≧ da
- mounting diameter in the housing ≦ Da
Tolerances for shaft and housing bore
Proven tolerances are given in ➤ Table . If the data are observed, this will give correct radial guidance of the bearing elements.
Tolerances for shafts and housing bores
Bearing component |
Tolerance class for |
||
---|---|---|---|
Shaft |
Bore |
||
Axial cylindrical |
Shaft guided |
h8 |
‒ |
Housing locating washers |
‒ |
‒ |
H9 |
Shaft locating washers |
‒ |
h8 |
‒ |
Bearing washers |
Externally centred as housing locating washer |
Shaft released |
H9 |
Internally centred as |
h8 |
Bore released |
- The envelope requirement Ⓔ applies.
Guidance of bearing parts
Release of shaft and housing locating washers, as a function of centring
If the bearing washers are centred on the shaft, they must have radial clearance in the housing bore while, if they are centred in the housing, there must be radial clearance between the washer bore and the shaft ➤ Figure.
Guidance and release of shaft and housing locating washers
|
![]() |
Guidance of axial roller and cage assemblies
In order to give the lowest possible sliding speeds on the guidance surfaces, the axial cylindrical roller and cage assemblies are in general guided on the shaft. This is particularly important in the case of high speeds.
For a direct bearing arrangement of roller and cage assemblies: harden and grind the raceways for the rollers
If the axial design space is particularly small, axial cylindrical roller and cage assemblies can also run directly (without axial bearing washers) on the adjacent construction. In this case – and if the load carrying capacity of the axial cylindrical roller and cage assemblies is to be fully utilised – the raceways on the shaft and in the housing must be produced as a rolling bearing raceway or must correspond to the quality and hardness of axial bearing washers. The surface hardness of the raceway must be 670 HV to 840 HV, the hardening depth CHD or SHD must be sufficiently large ➤ link. The surface roughness Ra must be ≦ 0,2 μm. At a mean roughness value of Ra > 0,2 μm, it is no longer possible to utilise the full load carrying capacity of the bearings. When designing the raceway on the shaft and in the housing, the raceway dimensions Ea and Eb must be observed ➤ dimension table. If the values are observed, this will ensure that the raceways for the cylindrical rollers – taking account of any possible axial offset of the roller and cage assembly – are adequately dimensioned.
Mounting and dismounting
The mounting and dismounting options for the bearings must be taken into consideration in the design of the bearing position.
As the bearings are not self-retaining, they are easy to mount
Axial cylindrical roller bearings are not self-retaining. As a result, it is possible to mount the bearing parts (shaft locating washer, housing locating washer and axial cylindrical roller and cage assembly) separately from each other. This gives simplified mounting of the bearings.
Mounting position of the bearing washers
The correct mounting position has a considerable influence on the function of the bearing arrangement. Axial bearing washers must always be mounted with the raceway side facing the rolling elements.
Shaft locating washers
On shaft locating washers, the raceway side is indicated by the smaller chamfer on the bore diameter of the washer.
Housing locating washers
On housing locating washers, the raceway side is indicated by the smaller chamfer on the outside diameter of the washer.
Schaeffler Mounting Handbook
Rolling bearings must be handled with great care
Rolling bearings are well-proven precision machine elements for the design of economical and reliable bearing arrangements, which offer high operational security. In order that these products can function correctly and achieve the envisaged operating life without detrimental effect, they must be handled with care.
The Schaeffler Mounting Handbook MH 1 gives comprehensive information about the correct storage, mounting, dismounting and maintenance of rotary rolling bearings http://www.schaeffler.de/std/1B68. It also provides information which should be observed by the designer, in relation to the mounting, dismounting and maintenance of bearings, in the original design of the bearing position. This book is available from Schaeffler on request.
Legal notice regarding data freshness
The further development of products may also result in technical changes to catalogue products
Of central interest to Schaeffler is the further development and optimisation of its products and the satisfaction of its customers. In order that you, as the customer, can keep yourself optimally informed about the progress that is being made here and with regard to the current technical status of the products, we publish any product changes which differ from the printed version in our electronic product catalogue.
We therefore reserve the right to make changes to the data and illustrations in this catalogue. This catalogue reflects the status at the time of printing. More recent publications released by us (as printed or digital media) will automatically precede this catalogue if they involve the same subject. Therefore, please always use our electronic product catalogue to check whether more up-to-date information or modification notices exist for your desired product.
Further information
In addition to the data in this chapter, the following chapters in Technical principles must also be observed in the design of bearing arrangements: